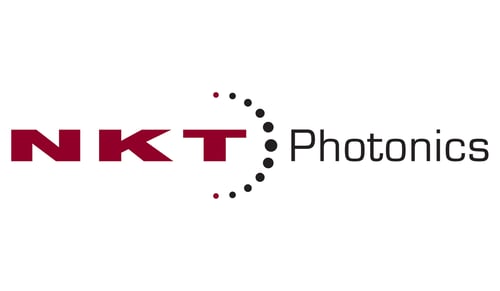
How NKT Photonics Eliminated Bond Failures with Surface Intelligence
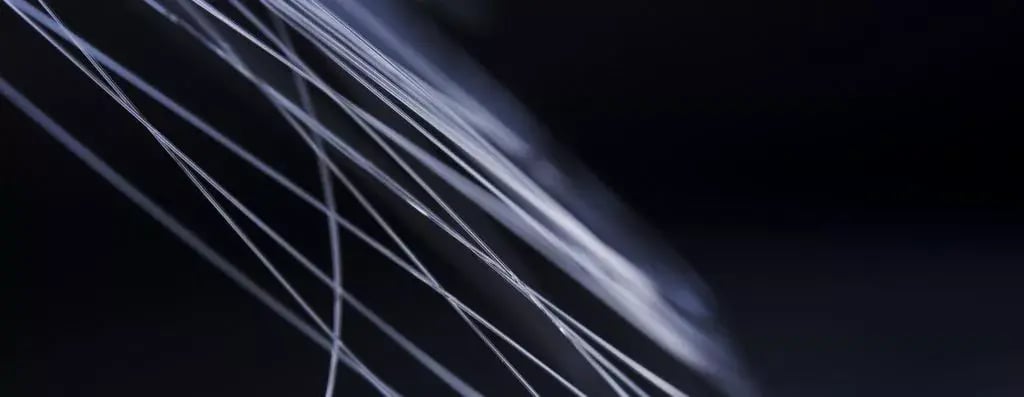
Industry
Photonics
Challenge
When NKT Photonics was forced to internalize its aluminum etching and surface preparation processes after losing a supplier, the transition led to unexpected bond failures. Despite duplicating the equipment and processes, the failures persisted, resulting in significant financial loss and reputational risk.
Results
Implementing Brighton Science’s BConnect system empowered NKT to identify and address inconsistencies in part cleanliness and surface quality caused by contamination and complex part geometries. Their data-driven approach to surface quality resulted in precise, targeted adjustments – within a year NKT completely eliminated their bond failures and established ongoing quality monitoring. With BConnect, NKT has implemented a more robust cleaning protocol, 100% inspection of parts prior to bonding, and increased shear strength up to 2x.
Key Product
BConnect Lab Network, BConnect Process Monitor
Just the peace of mind of knowing that everything's been measured...it's huge
Francis Guay
Manufacturing Engineering Manager
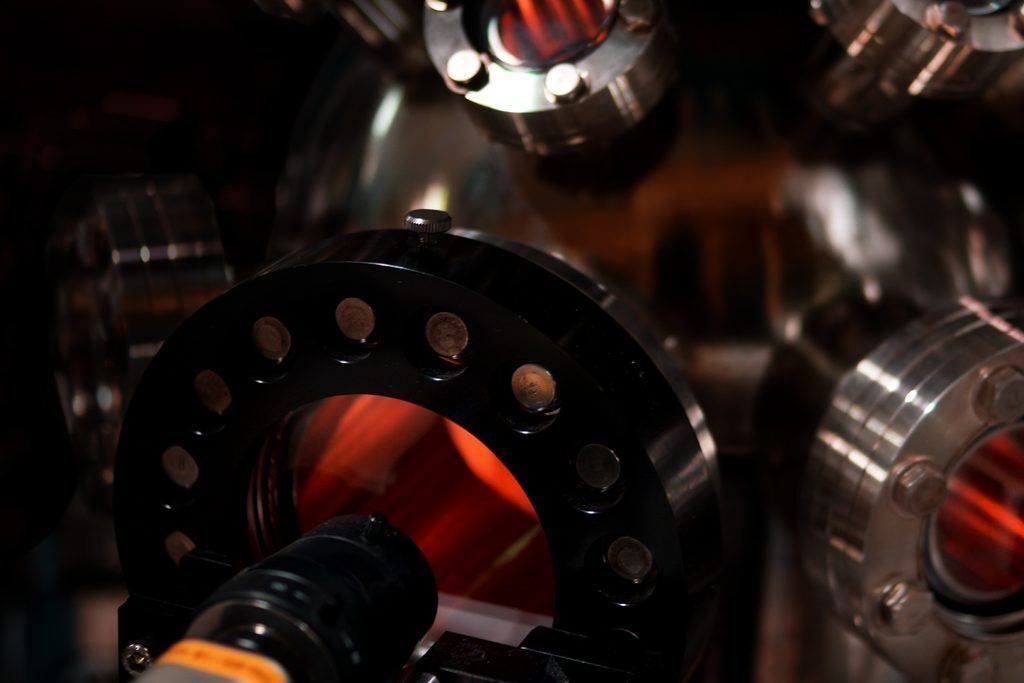
About NKT Photonics
NKT Photonics is a global leader in high-performance fiber lasers and photonic crystal fibers, serving industries like Medical & Life Science, Industrial, Aerospace & Defense, and Quantum & Nano Technology. With over 20 years of innovation, their lasers power everything from space missions to medical diagnostics, enabling breakthroughs in fields like quantum computing and renewable energy.The Challenge
When NKT was unexpectedly cut off from an external supplier, the team was forced to internalize their aluminum etching and surface preparation processes. Though the NKT team worked directly with the supplier to obtain the same equipment and duplicate the process as closely as possible, the transition led to bond failures.
These bond failures represented a serious problem for NKT – product returns from the field damaged company reputation, and the financial impact reached into six figures.
The Solution
After researching industrial solutions for surface quality testing, NKT discovered Brighton Science and the BConnect system. Key features that distinguished BConnect as the best solution included:
- Speed of measurement - The ability to take measurements in under three seconds allowed for real-time process monitoring.
- Portability - The compact instrument could be deployed directly on the production line.
- Precision - Consistent drop volume and deposition created reliable, repeatable measurements.
- Versatility - The compact, customizable measurement head could access complex geometries and difficult angles.
- Data integration - The API capability allowed surface data to be incorporated into NKT's process database.
Equipped with their new technology, NKT implemented BConnect in two phases:
- First investigating the source of bond failures, before using those insights to refine and validate their new surface preparation process.
- Then deploying it as an online quality control tool for real-time monitoring and 100% inspection of high-value parts.
BConnect empowered NKT Photonics to eliminate costly failures, standardize quality, and unlock continuous process improvement—delivering transformative ROI and long-term competitive advantage.
The Results
Using BConnect, NKT Photonics uncovered critical surface quality issues that had previously gone undetected, including inconsistent contact angles across complex geometries and ineffective cleaning due to varied machining fluids from different suppliers. Detailed surface mapping revealed that areas like corners and tapped holes retained contaminants, even when flat surfaces appeared clean. With this insight, NKT developed a universal cleaning protocol, implemented 100% inspection for high-value parts, and adjusted their cleaning parameters to ensure consistent surface preparation—resulting in zero bond failures for over a year and an increased shear strength up to 2x.
Beyond the technical gains, the ROI has been substantial. BConnect helped NKT eliminate costly rework and scrap, avoid six-figure losses from field failures, and standardize quality through real-time data integration and statistical process control. These improvements not only protect their reputation but also enable ongoing process optimization driven by objective, quantifiable data.