The Crucial Role of Conformal Coatings in Electronics
Electronic components are the backbone of modern technology, from implantable medical devices and navigational equipment to sensor packages in cars and everyday cell phones. These delicate and exposed pieces are vulnerable to various environmental factors, leading to damage and failures. That's where conformal coatings come into play. Conformal coatings are protective polymeric materials applied to electronic assemblies, such as printed circuit boards (PCBs) and electronic circuitry, to shield them from contaminants like moisture, dust, and chemicals.
By forming a uniform barrier around the components, conformal coatings ensure that no external impurities can reach the electronics, preventing issues like rusting, oxidation, dendrite growth, or other forms of corrosion. This protective layer is critical for maintaining the reliability and longevity of electronic devices, particularly in harsh environments. However, the effectiveness of conformal coating relies heavily on the cleanliness of the surface to which they are applied, making surface preparation a vital step in the coating process.
Understanding Common Conformal Coating Failures
Despite their importance, conformal coatings are not immune to failures. Various types of adhesion failures can occur, each compromising the integrity and functionality of the coated electronic components.
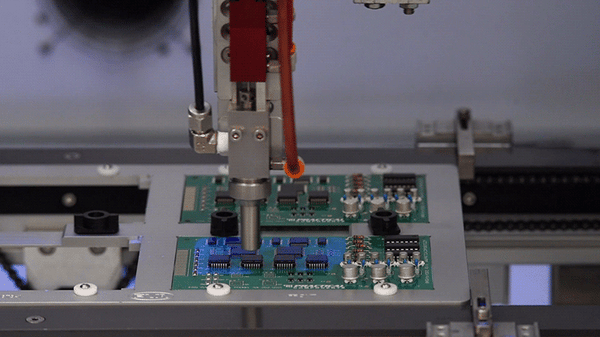
Common conformal coating failures include:
- Blistering - Cracking within the coating or at the interface with the board's surface.
- Blushing - A blotchy, milky, or clouding appearance due to contamination or uneven coating.
- Capillary Flow - The coating pulls back or runs from specific areas, leaving a patching finish.
- De-wetting - The coating "refuses" to fully cover a surface despite being evenly applied everywhere.
- Delamination - The coating lifts away from the board's surface.
- Discoloration - Color changes that can affect temperature response or component identifications.
- Fish Eyes - Localized de-wetting manifesting as small craters on the coating surface.
- Orange Peel - An uneven, textured surface, similar to fish eyes.
These failures are often preventable with a controlled adhesion process. Key factors in managing this process include the composition of the coating material, the application and curing process, and, crucially, the cleanliness of the bond surface.
The Importance of Surface Cleanliness for Coating Success
The cleanliness of the surface being coated is paramount to achieving reliable adhesion. Contaminants on the surface can prevent the coating from forming a strong bond, leading to the failures mentioned above. However, surface cleanliness goes beyond visible dirt or debris. It involves chemical cleanliness, ensuring the surface is chemically compatible with the coating material.
Most electronic components are made of polymers with intrinsically low energy, meaning they do not naturally bond well with coatings. These surfaces must be treated to create high-energy reactive sites eager to bond with the coating. Techniques like plasma, corona, or flame treatment can achieve this transformation.
Evaluating surface cleanliness involves understanding what contaminants are present, their sources, and how to measure a properly prepared surface. Traditional cleanliness tests like the ROSE test (resistivity of solvent extract) fall short as they only measure soluble ionic contaminants and ignore organic contaminants, which are more relevant to adhesion reliability.
Introducing Surface Intelligence: Measuring to Control
To control the adhesion process effectively, you must be able to measure surface cleanliness accurately. This is where the concept of Surface Intelligence comes into play. Surface Intelligence involves using advanced measurement techniques to understand the surface's chemical state at every stage of the adhesion process.
Ready to take control of surface cleanliness and adhesion reliability?
See how real-time measurement and monitoring can transform your coating and bonding processes. Download the BConnect Datasheet.
A highly effective method for assessing surface cleanliness is measuring the water contact angle. This technique uses a rapid measuring device integrated directly into the production line to provide real-time, objective data on the surface's readiness for coating. By identifying areas with chemical contamination that could lead to coating failures, manufacturers can take corrective actions before proceeding with the coating application.
How BConnect Enhances Surface Cleanliness Monitoring
BConnect is an innovative solution designed to enhance surface cleanliness monitoring and ensure optimal conditions for conformal coating applications. BConnect integrates seamlessly into the production process, providing continuous, real-time data on surface cleanliness. This data-driven approach allows manufacturers to maintain strict control over the adhesion process, reducing the risk of coating failures and ensuring high-quality, reliable electronic components.
By leveraging BConnect, manufacturers can:
- Monitor surface cleanliness at Critical Control Points throughout the production process.
- Identify and address contamination issues before they impact coating quality.
- Optimize cleaning and surface preparation techniques to achieve the highest levels of cleanliness.
- Ensure consistent, reliable adhesion and coating performance across all products.
Incorporating BConnect into the production process represents a significant step forward in achieving Surface Intelligence. It enables manufacturers to control what they measure and, ultimately, ensures the reliability of their conformal coatings.
Building a Predictable and Reliable Adhesion Process
Achieving a predictable and reliable adhesion process requires a holistic approach that considers all aspects of surface preparation, coating application, and process control. By focusing on surface cleanliness and leveraging advanced measurement techniques like water contact angle assessments and solutions like BConnect, manufacturers can build a robust adhesion process that minimizes the risk of conformal coating failures.
Key steps to building a reliable adhesion process include:
- Selecting the appropriate coating material for the specific application and substrate.
- Ensuring consistent and controlled application and curing of the coating.
- Implementing thorough and effective surface cleaning and preparation techniques.
- Continuously monitoring surface cleanliness using advanced measurement tools.
- Addressing contamination issues promptly to prevent coating failures.
By integrating these steps into the production process, manufacturers can enhance the reliability and performance of their electronic components, ensuring they meet the highest standards of quality and dependability.
In conclusion, conformal coatings' reliability is crucial for protecting electronic components in various applications. Surface cleanliness plays a vital role in achieving successful adhesion, and the concept of Surface Intelligence, supported by solutions like BConnect, provides the tools needed to monitor and control this critical aspect of the coating process. By adopting these advanced techniques, manufacturers can ensure that their conformal coatings deliver the protection and reliability required in today's demanding environments.
Stronger bonds. Higher quality. Greater reliability.
To learn more about how to increase electronics reliability by controlling surface quality from the start, download our eBook: Electronics Manufacturing: The Complete Guide to Implementing a New Approach to Increase Quality