The Advanced Guide to Transforming Product Development Through Surface Intelligence Data & Technology
Contents
How to Build a Standard for Surface Quality That Breaks Down Silos Within Your Organization and Across Your Supply Chain
One of the many goals of product development teams is to uncover downstream problems before product launch by identifying variables and isolating issues. This is hopefully captured in the DFMEA process. However, many times surface condition is not accounted for in the FMEA process. Why? Because what gets added to the FMEA is dependent on the expertise or experience in the room.
Since surfaces typically aren’t identified as important or risky areas (due to the difficulty of measuring them in production in the past) they don’t get added as something to carry risk. The truth is, these onerous variables inevitably reveal themselves once you start prototyping and especially when larger production runs are underway. So, it behooves teams to catch problems early and catch them fast.
New product and process development requires a heavy investment from companies and comes with significant risks.
Failure to control material surfaces early on amplifies risks such as:
- Extended time to market
- Endless testing that never supplies a solution
- Market loss
- Increased waste
- Recalls
- Damage to brand credibility
The best-kept secret in product development is that successful adhesion relies on the understanding of material surfaces at a fundamental level to:
- Incorporate innovative new materials with confidence
- Select the best adhesives for their application
- Seamlessly transfer new products from R&D or concept to production
- Eliminate using resources on unnecessary production issues
- Reduce supply chain disruptions due to unidentified surface variability
- Deliver high-quality products that reflect consumers demanding expectations
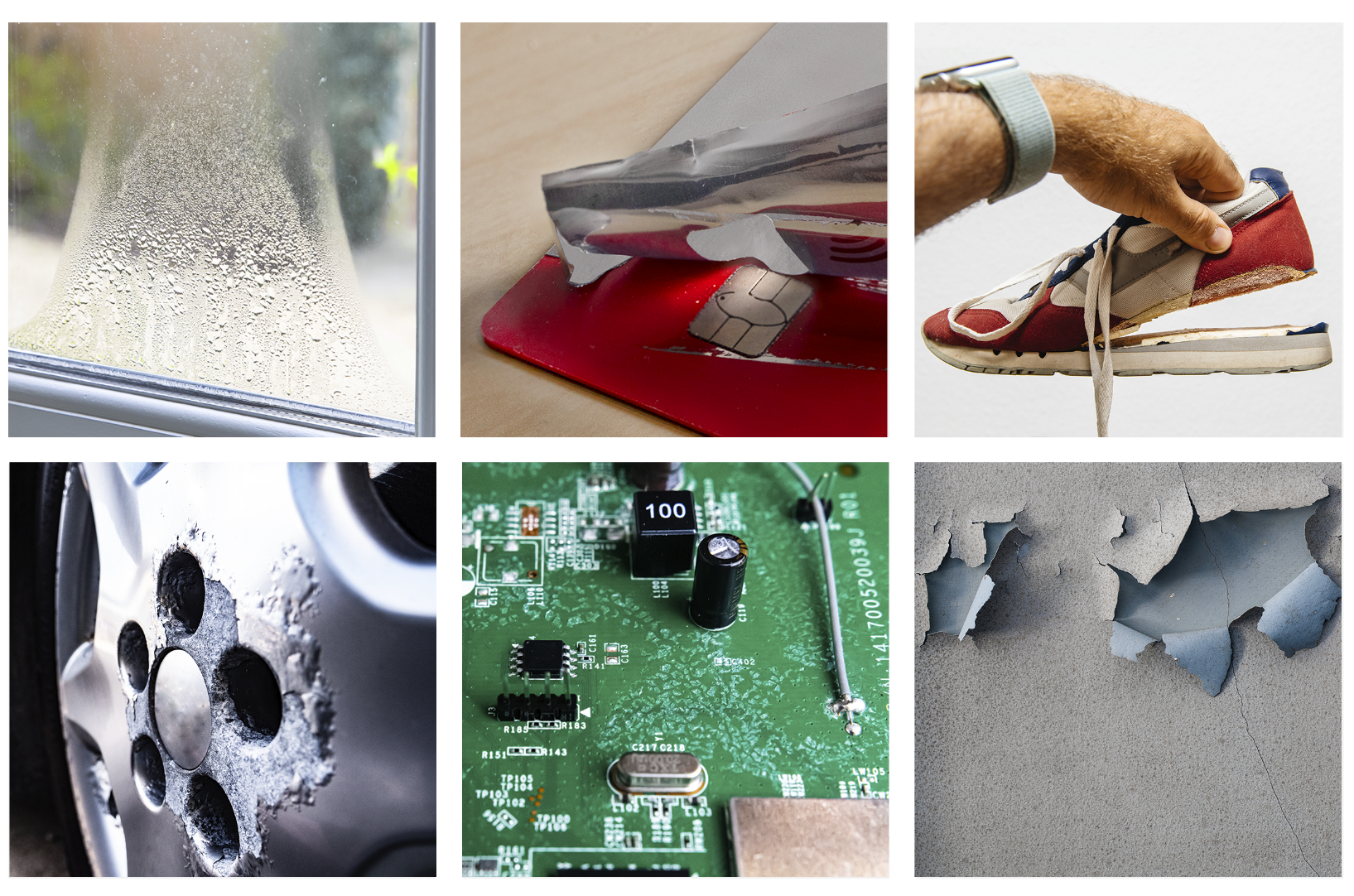
Download Your Copy
of This eBook
This eBook describes how organizations can leverage surface intelligence and technology to transform the way product development teams approach surfaces.
By leveraging surface intelligence, your business can control critical areas of risk that impact the time and quality of new products.
Download your copy of this eBook by completing the form.
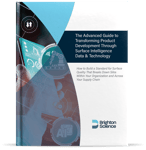
Optimize the power of next-gen connectivity with data & surface intelligence.
Unfortunately, it can be very challenging to manage surfaces, adhesion processes, and cleaning programs throughout the product life cycle in any industry.
Naturally, it all starts at the beginning. When a new product is still in the development phase, materials and processes for assembly are being determined. If these determinations do not include comprehensive testing around surfaces during creation, surface preparation methods that go for design for manufacturability (DFX), and the right performance tests then the product development is incomplete.
Material and process standards (that then flow to Quality specifications for surfaces) must be determined at the beginning of product development in order to control those surfaces throughout the manufacturing process.
This surface quality specification provides a common language for teams throughout the product’s lifecycle— starting with the supply chain, extending through R&D and product development, all the way to mass production. When teams do not have a uniform way to speak about surface issues, it opens the door to product failure without a way of knowing where to look to solve the problem.
How can product development teams implement a common language and increase predictability and reliability?
Let’s begin by breaking down the challenges that commonly occur in each stage of the manufacturing process and explore ways to combat them.
4 Common Surface-Related Problems to Avoid in Research & Development
For businesses to stay competitive, they require their R&D teams to provide innovative and high-reward research and insights to the organization. This process is necessarily expensive and time-consuming because when critical decisions about products are thoroughly assessed early on, product development teams can stop issues before they even begin.
1. Neglecting to Baseline Surfaces When Identifying Future Materials & Adhesives
When R&D teams fail to measure the surface quality of material while selecting adhesives and coatings that will be applied to those surfaces, an essential aspect of the process has been overlooked. Often, R&D teams choose adhesives and coatings based on sample testing. They take a material sample, conduct a cleaning step, apply an adhesive, and measure the bond strength. This bond strength testing occurs in a laboratory or controlled setting and assumptions are made based on conditions that do not reflect the real-world environment where the assembly will take place. Critical decisions are made according to these testing results, the effects of which, ripple throughout the rest of the manufacturing process.
They then proceed to build product prototypes, which is where issues begin to reveal themselves. The prototypes start to break down because the adhesive is the only element the R&D team controlled. The variety of contaminants in a manufacturing setting that can alter a surface at the molecular level, and therefore influence the reliability of an adhesive bond, were never considered. So, once those variables are introduced, the likelihood of product failure increases significantly.
By baselining surface quality at the earliest possible stage using a quantitative surface quality measurement, R&D teams can avoid the headaches of repetitive prototyping and incessant product failures as larger batches are built.
Moreover, manufacturers may inadvertently underrate an adhesive because failures are occurring that have nothing to do with the quality of the adhesive itself. This happens when adhesive bonding and cleaning processes aren’t intentionally tested, measured, and adequately developed during the sampling process using a surface quality measurement. This allows the team to know definitively if the material’s surface has been uniformly prepared before the adhesive is applied and then make modifications to the cleaning process as opposed to unknowingly disqualifying an excellent adhesive.
The job of qualifying adhesives can be a challenge. Teams often focus their time and testing on performance requirements rather than allocating time to managing process excursions and designing for optimal manufacturability. By focusing on surface quality during adhesive selection, teams allow the material’s surface to set the bounds of bond performance rather than the other way around.
2. No Standard for Surface Quality
An objective and measurable surface quality specification offers a unifying language across an organization to accurately discuss issues that arise around bonding, adhesive selections, cleaning processes and a host of other material surface-related aspects of manufacturing.
A lack of continuity leads to inconsistent results, burned-out development teams, and wasted time and money.
3. Applying Adhesives to Inconsistent Surfaces When Trialing New Formulations
When trialing new adhesive formulations, there is a general lack of awareness of how sensitive surfaces are to contamination. When you’re not able to know that a surface was prepared correctly it leads to an inconsistent surface, which means, the adhesive may be able to bond well in some places but not others, but it’s anyone’s guess as to where the difference is.
To avoid this guessing game, a thorough surface quality measurement gives teams the assurance they need to apply adhesives to consistent surfaces when trialing new formulations. Doing this will ensure that the adhesive has a chance to perform as intended. Furthermore, it will make it easier to identify any issues that may arise during the trial process.
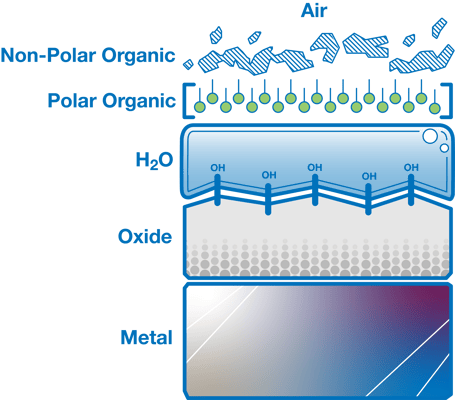
Figure 1: Demonstrates layers of contamination on top of the bulk material (metal).
4. Not Accurately Measuring Surface Quality
Organizations may not think that surface quality is all that important, but it can significantly impact the function and durability of their product. If they’re not creating a surface quality specification to pass on to their New Product Introduction and Design for Manufacture teams, then they are passing on imperfections caused by the manufacturing process itself, the materials used, or even the environment in which the product will be used.
They can get ahead of these imperfections with a precise surface quality specification that considers all these factors. Otherwise, they risk their product not meeting customer expectations or failing outright.

Surface-Related Challenges in Product Development and
New Product Introduction (NPI)
Because the quality of a surface is essentially invisible to teams that do not measure it, surface-related problems lead to unnecessary firefighting.
For example, New Product Introduction (NPI) teams may acquire unreliable results from their testing, making it impossible to determine which factors are causing the issues they’re seeing. Surfaces play a significant role in failure modes, and as a result of a lack of measurement, NPI/launch teams, process engineers, and others are left doing guesswork, self-diagnosing, and performing extensive failure analysis testing.
When the guessing starts, the team can spiral out as they question the entire assembly and ask themselves:
- Is the entire assembly bad?
- Does the adhesive need to be changed?
- Do we need to change the materials?
- Is a plasma system needed for surface preparation?
- Do we need to go back and change the actual design of the product or component?
Where does it end?
Unfortunately, this usually happens during inopportune times that may lead to a full shutdown of a manufacturing line or even a plant.
Without a quantifiable specification, teams cannot definitively understand the quality of their material surfaces and resort to costly trial and error, over and over again.
Rethink your adhesion manufacturing processes with Surface Intelligence.
Surface-Related Problems in Mass Production
Once the product has gone through NPI - where too many members have likely spent too much time working out the kinks - the manufacturing specifications and standard procedures are then handed off to production and quality teams. Ideally, the goal for this step is a “clean” handoff. From here, it’s expected that the quality team will use the specifications that NPI or the development team established to hold their suppliers and contract manufacturers accountable.
Although, specifications concerning surface quality are rarely devised when they should be, if at all, manufacturing, engineering, and quality teams are under tremendous stress to quickly fix the problems while actually building the product. In addition, manufacturing teams’ troubleshooting process is riddled with guesses and rework since they don’t have the data or resources they need to do a holistic root cause analysis.
So, manufacturing and quality teams are left frantically working to change variables within the process to see what will fix the issues. Changes could include swapping out the chemistry of the washing fluids, adding additional cleaning steps, investing in new surface treatment equipment, manufacturing or cleaning processes, or cycling through a myriad of different adhesives.
These common issues result from a poorly defined and executed product development life cycle. Failing to implement a surface quality standard as early as possible turns what is intended to be a proactive process into a reactive and slow one.
Surface-Related Issues in the Supplier Ecosystem
Many challenges come with the working relationships of suppliers, OEMs, and contract manufacturers, including process compliance, uniformity of quality, and communication.
The supplier ecosystem can be isolated from the rest of the manufacturing process, making it difficult to trace issues back to the supply chain. When the OEM doesn’t have an easy-to-use and clear standard, it results in the OEM paying for it later, typically in the form of rework, failure, scrap, and other costly measures that can be avoided by bridging the supplier ecosystem to the greater production process with a common language of surface quality and measurement.
Suppliers and contract manufacturers are usually not experts in surfaces – nor should they be. The OEM that does a good job of creating a common language around material fundamentals will make everyone’s job much easier. Questions surrounding surface state, how to create it, how to keep it, and how to deliver it need to be things of the past.
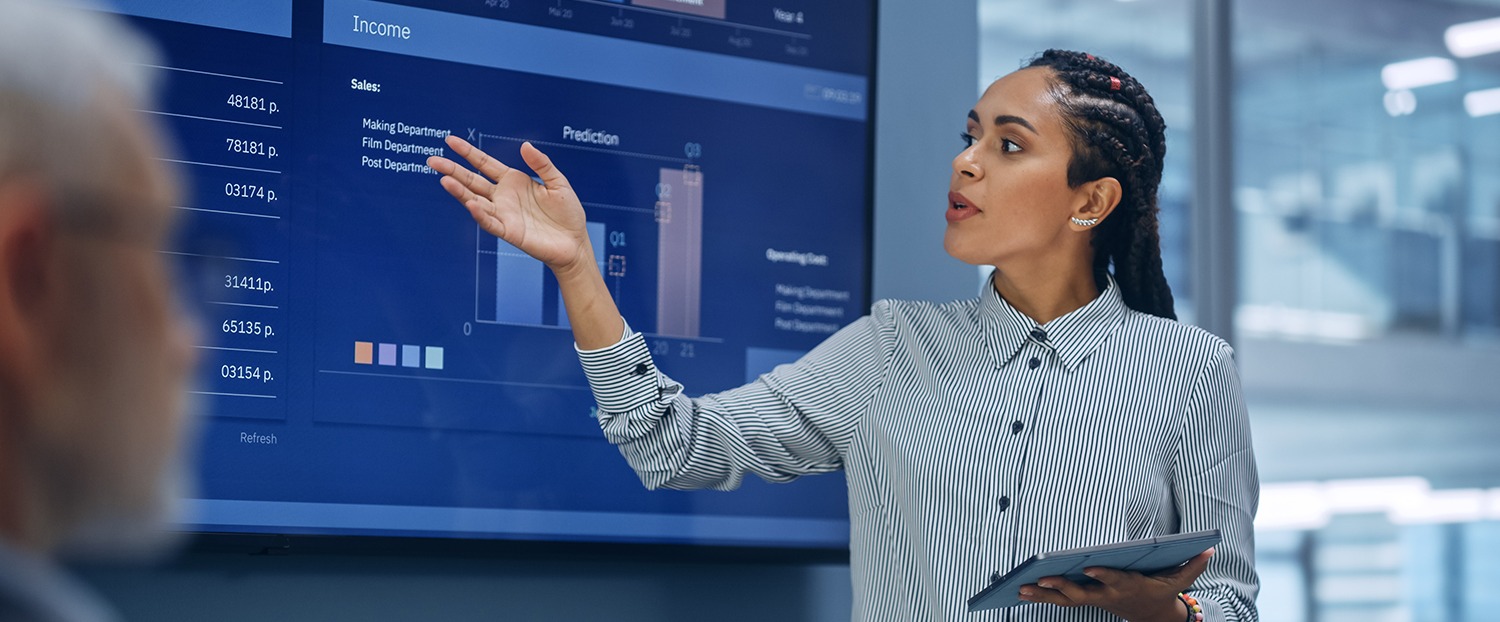
Download Your Copy
of This eBook
This eBook describes how organizations can leverage surface intelligence and technology to transform the way product development teams approach surfaces.
By leveraging surface intelligence, your business can control critical areas of risk that impact the time and quality of new products.
Download your copy of this eBook by completing the form.
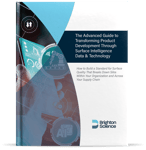
How to Find the Correct Solution for R&D
When a company is looking to improve its product development process, it often turns to R&D to find the right solution.
Specification Development
A surface quality specification is comprised of various parts, including material descriptions, options for material selection, performance and testing criteria, testing equipment, and more. Once a successful surface quality specification has been developed based on measurements and analysis, it can then be passed downstream to the rest of the individuals responsible for launching the product. This specification breaks down communication and information silos often created when processes aren’t fully understood.
A specification and common language for discussing surfaces allow teams to know without a doubt what the surface quality levels should be when test specimens are built.
Performance Testing
When looking at a potential new adhesive, it is vital to consider its physical properties and performance. How will this product stand up to the intended use? What are the consequences if it fails?
Do you have the correct performance tests? Many teams do not know how to effectively evaluate bonds and adhesive systems in a way that offers the most useful data. It’s essential to work with qualified experts who can answer these questions in detail and have a deep understanding and experience in materials and processes. Working alongside surface quality experts will deliver a critical understanding of every variable that needs to be considered by R&D teams to free them from relentless, ineffective testing.
Additional critical points to consider include failure MODE, failure load, and durability when mapping performance. Lap shears are fast and easy, but are they the best test that will give you the information you need? How are you evaluating durability? These critical questions must be answered to successfully test for performance.
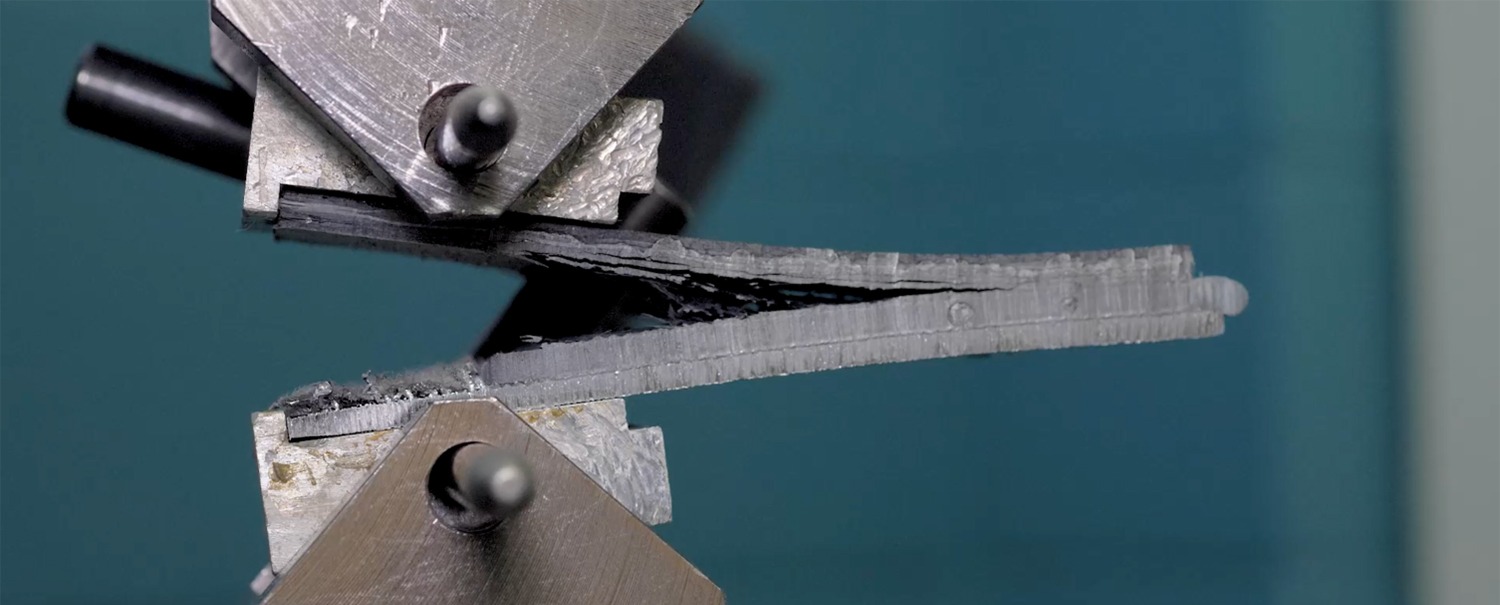
Figure 2: Adhesive bond testing
Material Selection
The key to selecting materials is understanding how they will interact with each other in real-world environments and what cleaning processes are best suited to get optimum results from specific materials. Water contact angle measurement and Surface Intelligence Data provide the most foolproof way to determine the best material for a particular application.
These novel data sources give manufacturers the confidence to work with new materials, advanced coatings, and adhesives because they can better control what happens to the surfaces of those materials. This allows them to make informed decisions about how to reevaluate the manufacturing process. Surface Intelligence data gives a fuller picture of how materials are changed by their environment and the manufacturing process, offering more predictable outcomes.
Process Selection and Optimization
By implementing surface quality standards and specifications, R&D teams can eliminate the constraint of variable surface conditions when selecting processes that will allow them to build the product. If teams are able to confidently know the state of their material surfaces at all times, they can select a process or method that will be the most optimal for how the product will be built. For example, how would an R&D team know the difference between plasma treatment and laser cleaning performance? What about manually wiping a surface versus putting into place an industrial washer? What supplier or assembler will produce the best quality results?
Surface Intelligence allows businesses to confidently adopt new design and process technology and prove their ROI based on real, quantifiable data.
For the product’s lifecycle to go according to plan, product development teams need R&D (or a material team) to give consistent and high-quality information at the beginning.
The ideal material and process selection must incorporate a predictive model for success. By using solid scientific backing for quick screening of materials and processes the product development timeline can be shortened. Select the right adhesives, the right substrates, the right prep methods, and the right performance tests to rapidly build your model.
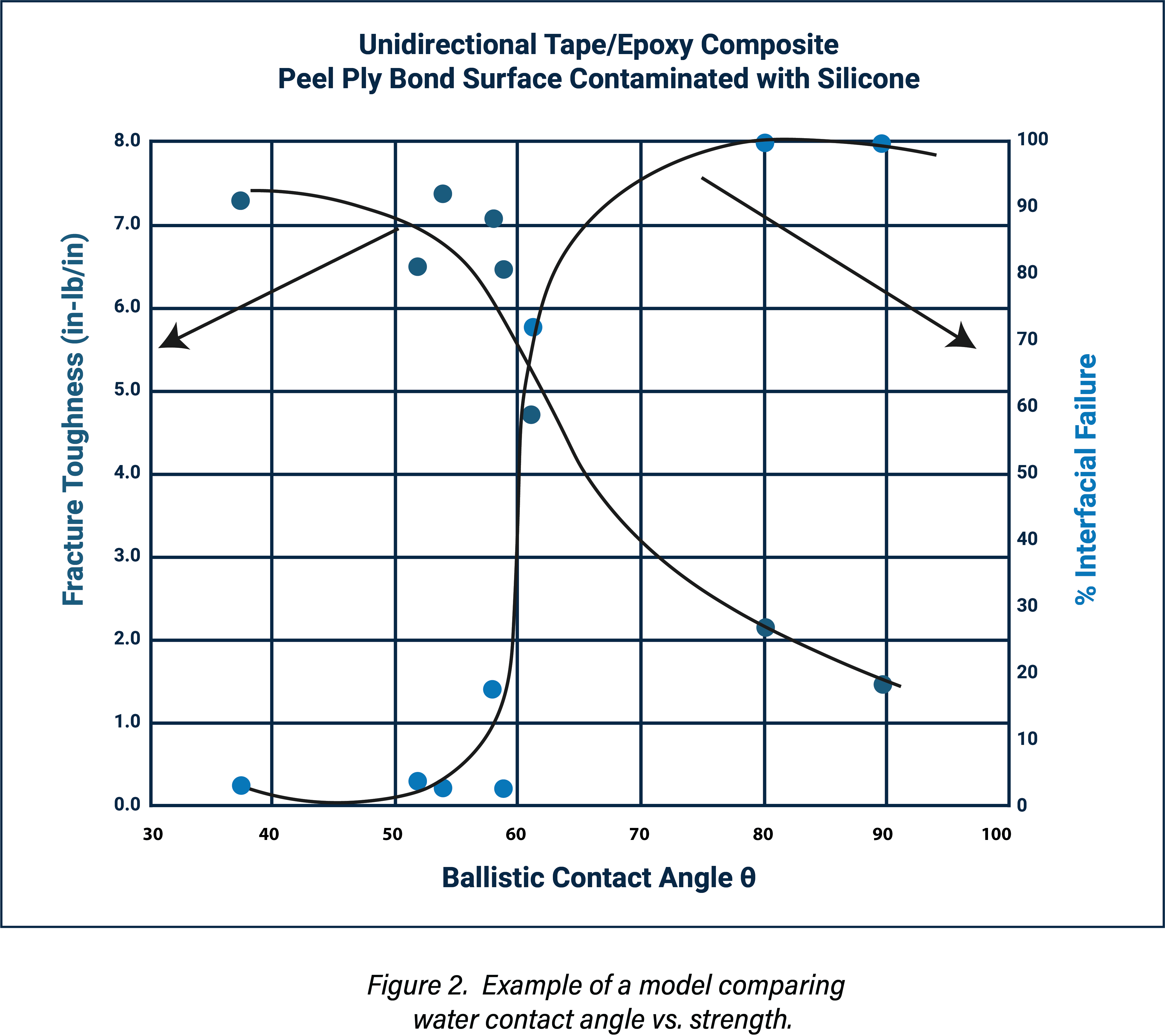
What Does the Ideal Solution Look Like for NPI?
The ideal solution for NPI is a well-defined workflow design and pilot manufacture that includes surface quality specifications.
The specifications established by R&D to baseline the surface quality of prototypes and EVT/DVT builds are essential to the process. Not only will it save time that often goes to troubleshooting issues, but it also provides a strong foundation to measure the success of future design changes. By removing surface quality variability from design changes during reliability testing, teams can more accurately determine what is causing any additional issues.
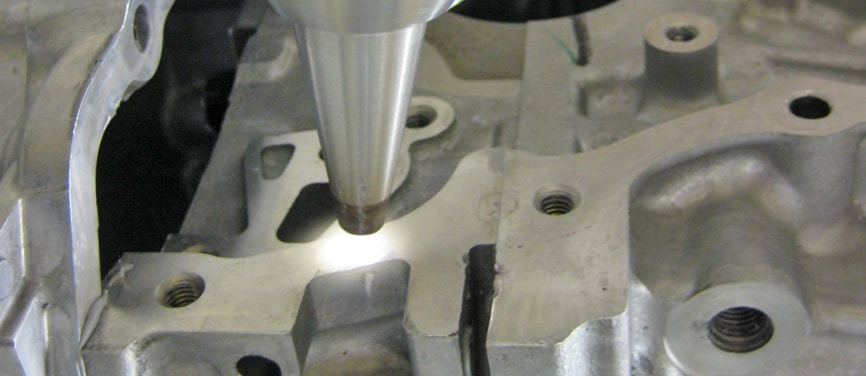
Image: plasma treatment on an automotive part.
Finally, by working on other aspects of assembly to minimize compromises, teams can avoid making too many trade-offs in the design and manufacture of the final product.
Using this method, teams can iron out the kinks in NPI and establish a clear, repeatable manufacturing specification. Then, the specification is handed to the quality team and used to hold their suppliers, vendors, and contract manufacturers accountable.
Teams will avoid spending countless hours troubleshooting, last-minute trips to global manufacturing and testing sites, and phone calls at 3:00 AM to determine the root cause of adhesion issues.
Implementing a surface measurement tool that accurately captures data to build a quality specification enables teams to ultimately do less failure analysis because they can easily interpret the data more precisely and with a smaller margin of error.
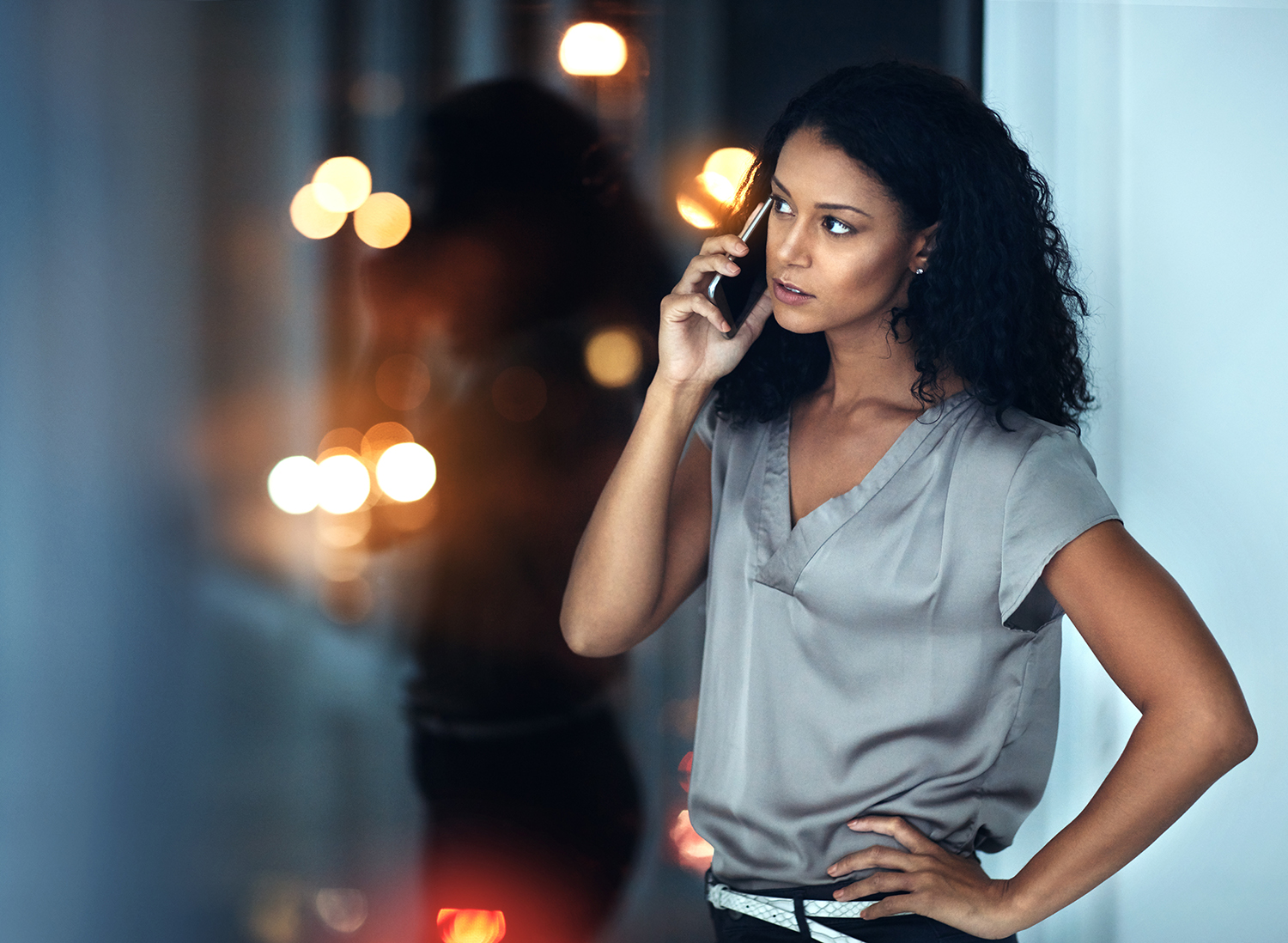
How Does Surface Intelligence Solve Product Development Issues?
Without proper control and management of material surfaces from the beginning, surface-related issues compound with each step of the product life cycle. By the time the product is entirely manufactured and ready to ship to the end customer, problems that haven’t been dealt with have become extremely expensive to fix, or they simply slip past and enter the field creating significant risk to every business involved and their brand image.
Businesses can use surface intelligence data to generate surface specifications, enable teams to select quality vendors and establish new communication protocols and ways of confidently understanding what is happening with their material surfaces.
Process Maintenance & Yield Optimization
Using Surface Intelligence data, teams can maintain processes and increase yield by optimizing processes, so they’re always “in spec” and running at the highest performance possible. This could involve everything from real-time process monitoring, to adjusting parameters, to analyzing past data to find trends and optimize for them.
Establishing Standards to Ensure Consistency Across the Supply Chain
Establishing standards reduces warranty claims and returns and helps to maintain a premium brand image. The ability to easily monitor data on surfaces for critical bonds/coatings allows SQE teams to build reliably bonded products for customers, whether it’s the first or 100,000th build.
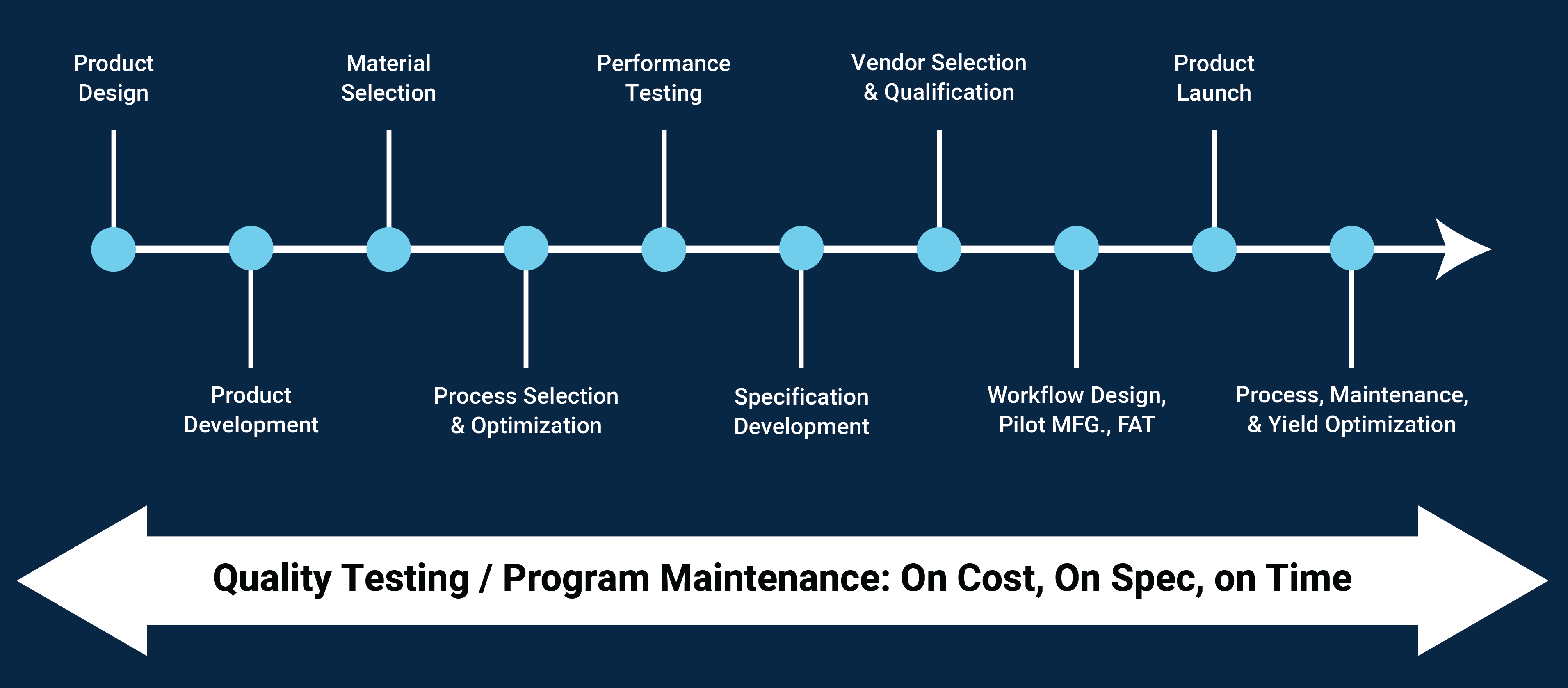
Creating a Common Language Internally and Across the Supply Chain
The recommended approach to creating a common language internally and across the supply chain, OEMs, and contract manufacturers regarding surface quality and specifications, is to work with Surface Intelligence experts at the beginning of the process.
Doing this will ensure continuity and communication throughout the entire process, from R&D to final production. It begins with the initial evaluation of materials and adhesives, which manufacturers will then apply to their products.
Product developers must answer the question, “What do I need to know?” Working with Surface Intelligence experts will help you find the answer to the following critical questions:
- What does the final product’s performance in the field need to be?
- What are the performance specs needed for joint design, and how strong, durable, and tough does it need to be?
- Can you predict how an adhesive will perform in the field, in harsh environments, or after years of wear and tear?
- Can you properly test how the interface between two materials will perform in end-use conditions?
- Can you define the quality of the materials and know when they are out of spec?
The only way a team gets to be able to address problems with the right solution is with information. It gives them ultimate flexibility. However, this only happens if you have the correct measurements.
How are Businesses Trying to Address Problems Today?
Typically, manufacturers rely on the raw material supplier for the substrate or the material supplier of the chemistry they apply to the surface.
But neither one is an expert in the other’s area and is not invested to the same degree as the customer. The material or adhesive supplier may advise the customer, but they typically will not take ownership of the problem.
One solution is to contract a high-end test laboratory to determine the issue. This option can be expensive, but getting an expert opinion will be worth it in the long run.
Struggling with adhesion failures? Been there. Solved that.
How to Find the Right Provider with the Right Solution
It is recommended that R&D and product development teams look for a partner with expertise in materials and processes and the entire product development lifecycle. Businesses should work with a partner who is not just an equipment provider but one who looks at the challenge and solution holistically and can bring together product development, testing, manufacturing, surface intelligence data, and diagnostic tools to create a complete solution.
With surface quality data made readily accessible by surface measurement tools like the Surface Analyst and Brighton Science’s deep scientific and technical expertise, you’ll have access to unprecedented insight and intel. This gives you mission-critical decision information and a powerful competitive advantage.
Whether you’re troubleshooting on the production line or designing a breakthrough product in R&D, tasked with meeting regulatory requirements, creating solutions to increase throughput, specifying new materials, or identifying the root cause of an adhesion or bonding failure, Brighton Science is your partner in improved performance.
Learn how to leverage Surface Intelligence and surface measurement diagnostic tools. Download the eBook “Brighton Science Guide to Flawless Manufacturing.” With this cutting-edge information at your fingertips, you’ll be able to take your business to the next level!