“For every company, its competitiveness comes from its ability to assimilate knowledge and failure - which I tell my kids all the time - failure is an opportunity to learn and feedback is a gift. And if we take the 'quick fix' we take the learning off the table.”
Andy Reeher, CEO, Brighton Science
Instead of powering through manufacturing business “emergencies” because of a failed product in the field or a lower-than-acceptable yield of product, crippling your ROI for the quarter, adding a surface quality specification allows organizations to put reliable processes into motion from the very start.
It’s no secret that solving quality problems as early in the development process as possible increases the likelihood of building high-quality products. It’s the motivation behind strategies like failure modes and effects analysis (or FMEA). Understanding where risk resides in the process allows you to target those areas so they don’t affect the end quality.
It’s painfully clear when a thorough understanding of risk and holistic failure analysis didn’t happen early on. The problem reveals itself to the public when the gears of production are ground to a stop thanks to a chemically-unclean surface or an insufficiently bonded substrate.
In many cases, specifications are developed, prototypes are created, products move to mass production, and marketing and advertising content are created, yet the product isn't able to launch. This severely cripples a company’s return on investment (ROI), or the profit or loss each investment earns.
Rethink your adhesion manufacturing processes with Surface Intelligence.
Failure to Learn = Failure to (Successfully) Launch
Andy Reeher, CEO at Brighton Science, sat down with us to outline common “quick fixes” he discusses with other executives.
“[Any company] can solve the problem locally and solve it today, maybe even go back to the root cause … but the challenge there is that a technician solves the problem in Saint Paul [Minnesota]. That same problem might happen in Omaha, Nebraska, or Plymouth, Michigan,” Reeher states.
The root cause of the problem isn’t being researched, which becomes a catalyst for a multinational drop in communication. For example, if the technicians who solve the original problem neglect to share the solutions with their managers, when (not if) other plants encounter the same problem, that knowledge isn’t shared or even researched as to how it happened. In the end, that company hasn’t learned anything, and neither have the technicians.
A failure to educate all levels of employees will bleed into your eventual product launch. If your brand fails to launch successfully due to operational errors that could've been remediated in the product development stages, your credibility will suffer. And if your process is automated, like a majority of the automotive industry, finding a root cause becomes even more imperative.
The “Built Ford Tough” Example
Let’s look at a recent example of a company that failed to implement Surface Intelligence into their production process, Ford Motor Company, with their ever-popular Ford Bronco. Ford had a well-designed and exciting product, but due to a bonding challenge on some painted hardtop roofs, they experienced delay after delay. Ford even went so far as to promise replacement roofs and vehicles to customers who had already received the defective SUVs, decreasing their return on investment and eating into their profit margins.
Surface Intelligence - or a lack of it - directly correlates with a lower return on investment for companies.
This is a problem with a solution. Adhesion issues do not need to be discovered after the product has been assembled, coated, glued, or painted. Instead, it’s a risk that can be identified and remediated in the product development phase.
Instead of resorting to quick fixes when the root cause isn’t clear, companies can establish a surface intelligence-centered methodology to eliminate these issues from reoccurring. This inevitably results in greater profit margins with lower production costs and easier-to-meet metrics.
Without Surface Intelligence, Adhesion is Complicated
Take it from us: the science of adhesion can quickly become very complex. Yet, applying simple principles of surface intelligence, like Critical Control Points or a contact angle specification, turns adhesion into another manageable aspect of the manufacturing process that can be controlled and measured.
The key to understanding adhesion in a way that will allow you to control it is appreciating and understanding how delicate surfaces are.
Surfaces that will be adhered to must be prepared adequately – in terms of quality – on a molecular level. When the molecular makeup of the surface has been created to particular specifications, it will successfully interact with the chemistry being applied, whether it’s an adhesive, paint, coating, or ink. Success!
Figure 1: The molecular levels are hidden on the surfaces of your parts and items.
Tribal Knowledge and Outdated Testing Methods
Any material that will be adhered to needs to have its surface prepared for the chemistry of each adhesive or coating that will be applied. For many materials, like metals, there’s often legacy tribal knowledge within businesses about how to prepare the surface.
This knowledge might come from a vendor advising on which materials work best with certain chemistries or other materials they manufacture.
Often this knowledge is passed along through the industry because it’s the “solution” that’s historically been applied. Typically, these “fixes” include adding more solvent, switching the adhesive out for stronger chemistry, adding in a laser cleaner, using flame treatment, or any number of other legacy fixes that are a shot in the dark—guesswork, at best.
All these variables cause risk. Are you willing to risk your entire product and thousands, if not millions, of dollars on guesswork?
Between all these best guesses and the actual difficulty of talking about the true condition of the surface (in a way that considers the top few molecular layers), this is a complex problem to face. These issues show up as flux not flowing adequately on chipboards, paint failing to adhere to vehicle components (see Figure 2), bonded structures breaking earlier than expected, and many more.
Figure 2: Paint peeling on the rim of a wheel
These issues can be insidious and are often chalked up to the cost of doing business. Wouldn’t it be more prudent for the overall goal to increase ROI? Tribal knowledge hasn't fixed most of these adhesion issues, but they’ve become almost standardized in the business. Meanwhile, extremely high scrape rates have become normalized, turning your company further away from your bottom line.
Reeher adds that told testing methods like dyne ink or water break tests are still common practice in manufacturing processes, but each one manages to miss the mark in several ways (see Figure 3).
“I was talking to a CEO at a treatment company, and she said, ‘I watch our technicians do water break tests on our parts and as they come out of the parts washer [the technician] sprays it and look at the product. And then the next guy in the line [does the same thing], but does he look at it the same way?’
And I think that’s why being able to have objective measurements is so critical and why [Brighton Science’s] innovation has been so important in being able to drive quality out on the plant floor, not just in the lab,” Reeher recalls.
Figure 3: Contact Angle tests hit all the right marks, while outdated testing methods come up short.
Risk Isn’t Well Assessed
Trying to hit your KPIs for the year? You might be shooting in the dark if your product development teams don’t account for the conditions of the production environment. While implementing quality tests, make sure they’re asking the important (but often invisible) questions:
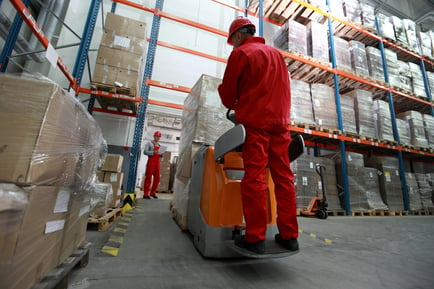
- What will the environment look like at the plant, and how might that affect our surface quality?
- How long might the materials sit in the warehouse before being assembled, and is their storage material a possible cause of surface contamination?
- How might our vendors change and impact the quality of our surfaces
"Surfaces are a frequently overlooked category of quality in a relationship between an assembler and a vendor.”
Andy Reeher, CEO, Brighton Science
Implementing surface intelligence at this early testing stage will quickly answer these crucial questions and ensure no problems arise from those parts of the process. To leave those critical aspects of production to chance is a costly error, one that will hurt your chances of hitting your KPIs.
A Lack of Knowledge and Training
Optimize your teams’ output by adding more training focused on materials and surfaces and you’ll also see an increase in common KPIs like an increase in labor efficiency and an increase in on-time delivery. Ignoring this knowledge gap directly affects quality and therefore hits the bottom line of companies that require efficiency and high production rates to stay competitive.
Surface intelligence includes a deep understanding of how sensitive surfaces are and how time impacts their quality. For example, a person on the manufacturing product line may clean the surface with a solvent and then set it aside for a considerable amount of time. While the material sits there, the surface actively changes and degrades.
In this scenario, it's not the front-line technician’s fault. They weren’t aware of how surface conditions can be altered so quickly simply when left alone.
Optimize the power of next-gen connectivity with data & surface intelligence.
The longer you wait to implement surface intelligence principles and knowledge, the more expensive the consequences are due to all the required backtracking. The earlier it’s factored in, the more likely you’ll be surpassing your annual metrics and your profit margins increased, not to mention a growing return on investment.
The ROI of Surface Intelligence is Clear
“[Regardless of the type of product or industry you’re in,] understanding early on, what surface quality standard you want to hit, measured by a number, is a key way to know if you’re going to be successful from both a cost and a quality standpoint.”
Andy Reeher, CEO, Brighton Science
Beginning your process with surface intelligence clarifies what's possible - what exciting things can be done with new materials with untapped potential that could increase revenue, increase operational efficiencies, lower production costs, lower downtime, and more.
During the FMEA stage, it’s critical to understand the risk areas for functions down the line, and it’s imperative to know how to describe the risks for those functions. Having a standard surface quality measurement that's objective and produces real-time data, along with commonly known information about how sensitive surfaces are, suddenly brings a zoomed-out perspective to the entire process. This can help developers begin to view production as an adhesion process because every decision made affects the surfaces that will be bonded to.
This is a much richer way of understanding the impact of choices made before committing to launching a product. Looking at material surfaces with knowledge and insight expands the toolbox of manufacturers. It also saves the organization monumental amounts of money due to lower scrap rates and operational efficiencies, resulting in higher product quality and more positive brand awareness.
Read how you can best account for surface readiness and all the positives that come with that choice ( more output, increased profit margins, and better material options) in our eBook, "The Advanced Guide to Transforming Product Development Through Surface Intelligence Data & Technology."
Experts Featured:
%20(1).jpg?width=183&height=183&name=andy-reeher-employee-photo%20(1200px)%20(1).jpg)