Manufacturers are increasingly utilizing a greater number of adhesive materials as a joining technique in the construction of their products, and the importance of these uses is continuously increasing with each passing year. As a result, the consequences of adhesive bond failures are becoming more costly. While users of adhesives understand that such failures can occur, they may not be aware of the underlying reasons behind them.
What are the Disadvantages of Adhesive Bonding?
One of the main causes of bond failures is the lack of detailed instructions provided by adhesive manufacturers regarding surface preparation and surface treatment prior to bonding. This raises the question: why don't adhesive manufacturers offer more comprehensive guidelines for the joining process?
One possibility is that they may believe it is in their best interest to portray their products as requiring minimal preparation - simply apply the adhesive to a clean, dry surface and wait for it to cure. Do you want to ensure your use of adhesives is successful? Simply apply a layer of primer, and voila! A successfully bonded structure is achieved!
These sorts of simplistic instructions neglect the fact that the quality of the bond depends intimately on the chemical composition of the surface being bonded and the chemical reaction between the surface and the adhesive.
The “surface” we’re talking about here is not what you see; it’s what you don’t see: the submicroscopic stuff on the surface that we call contaminants, which frequently can’t be removed without well-thought-out and controlled cleaning processes.
To ensure a successful bond, it is essential to understand what the adhesive's technical data sheets don't tell you about bonding. By learning about the composition of surfaces and how to clean or prepare them properly, users can avoid failures and create reliable and lasting bonds. Cleaning and surface preparation details are critical and typically specific to a particular substrate. They can also be specific to the supplier because materials from different suppliers will generally have different amounts and types of contaminants. These specifications will require different surface preparations to obtain a durable bond strength.
For example, a cleaning process that works well for material from “Supplier A," which uses a wax-based rolling lubricant in forming their aluminum, will likely fail when used on aluminum from "Supplier B," which uses silicone-based lubricants. This is because cleaning processes that frequently remove waxes or oils don't always work as well to remove silicone-based lubricants. This is just one example of how the instructions on technical data sheets can be overly simplistic when they fail to consider the wide variety of variables involved in surface preparation.
Contamination Affects Bond Performance
The type and amount of contamination on the bond surface can significantly impact the bonding process's success or failure. But even if the surface has been cleaned well, unintended contamination events can occur during the manufacturing process in the elapsed time between surface preparation and adhesive application. A cleaned part that sits for a few hours in the manufacturing facility can become unintentionally contaminated by things as seemingly innocuous as a passing forklift or an HVAC system circulating air from other parts of the plant where mold releases are being applied. These contamination events cannot be detected by the naked eye or through “white glove” tests.
The probability of an unintentional contamination event increases with each passing minute between surface preparation and bonding. Therefore, it is crucial to be aware of the potential for contamination and take steps to minimize the risk.
Rethink your adhesion manufacturing processes with Surface Intelligence.
Roughening the Surface Can Help When Bonding Materials, But...
Most adhesive data sheets include instructions to 'roughen the surface' to create a successful bond, and the instructions frequently imply that roughness is an important characteristic of a bond surface.
While roughness can certainly help make a good bond better, the requirements for strong and reliable adhesive bonds are more subtle than simply ensuring a rough surface.
Imagine a nicely roughened surface ready for adhesive bonding that gets accidentally exposed to a bit of mold-release mist that wafted over from another manufacturing cell. Although the roughness hasn’t measurably changed, the surface is now “unbondable” without a cleaning or pretreatment remediation step.
More important than roughening is to ensure that the surface is clean of contaminants. Furthermore, the cleaning needs to be performed prior to any roughening step. This is because abrading a contaminated surface of the bond area grinds contaminants into the nooks and crannies created by abrasion. These contaminants are now much harder to remove.
The best abrasion processes are ones that include three steps: precleaning, abrasion, and post-cleaning. The precleaning step, either aqueous cleaning with a high-quality rinse or solvent-based, removes the bulk of the contaminants. This abrasion step can remove any weak oxides and create a fresh, mechanically strong surface. (A rough surface can also re-direct crack growth away from the interface, making crack initiation more difficult and improving fracture toughness). The final post-abrasion cleaning removes debris generated by the abrasion process. These three-step processes can produce excellent surfaces for strong bonds and reliable coating.
In summary, while roughness can enhance a clean bond surface without ensuring molecular-level cleanliness (free of contamination), abrasion will only produce a mediocre adhesive bond surface at best.
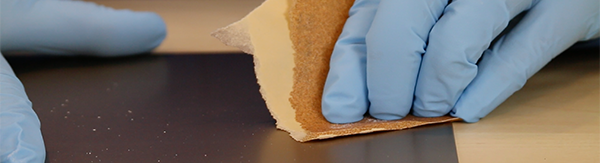
The Details of Surface Preparation Are Crucial
The amount of contamination that can interfere with adhesive bonding is so small that it is not visible to the eye or to a ‘white glove test.’ This means that preparing the surface well and consistently is highly dependent on the details of the surface preparation process. This can become a big problem for manual surface preparation processes when there are slight variances in how different operators implement cleaning methods.
Slight differences in technique, like how often cleaning cloths or abrasives are rotated, how much pressure is used during wiping, and whether the wiping process is linear or circular, can make a big difference in the performance of the final bonded structure.
This leads to the next question: How can the results of a surface preparation process be evaluated and compared besides the destructive testing of the final adhesive joint?
Control Of Surface Preparation Process Requires Measurement
The only way to ensure that a surface is adequately and consistently prepared or cleaned for adhesive bonding is to use a measurement technique that has versatility in use and is sensitive to the same low levels of contaminants that affect adhesion.
One particularly convenient technique is to measure the contact angle formed by a drop of water on the surface. Contact angles provide a precise and accurate way to measure a material's surface energy and immediately flag the presence of contaminants and substandard surface preparation.
Modern instrumentation (like the Brighton Science Surface Analyst™) provides fast and quantitative contact angle measurements on the manufacturing floor with a single button push, along with BConnect, a Surface Intelligence network that integrates the measurements into overall quality and process control systems.
How Adhesives Manufacturers Are Reducing Bond Failure Through Improved Technical Data Sheets
Leading adhesive manufacturers who recognize the subtleties of surface preparation and its effect on product performance put great value on quantitative control of adhesive bond surfaces. An example is Henkel, which now includes contact angle specifications in its Technical Data Sheets (TDS). This detailed and quantifiable product application guideline improves customer success and fosters stronger customer relationships.
Read how Henkel and Brighton Science partnered to establish surface measurement standards for their adhesive technical datasheets
Filling in the Gaps in Technical Data Sheets for Improved Bond Performance
Surface preparation for reliable, high-performance adhesive bonding and coating is a subtle and sensitive process. One size usually doesn’t fit all, meaning that, in reality, adhesive manufacturers would need a different TDS for every type of adhesive and their applications. To avoid this, most adhesives manufacturers err on the side of too little information and provide TDSs that are so general regarding surface preparation as to have almost no value.
An appreciation for the sensitivity of adhesive bond performance to the molecular-level cleanliness and composition of the bond surface and an awareness of tools like contact angle measurement for measuring and controlling this surface composition allows manufacturers whose product performance depends on bonded joints to ensure quality and improve the customer experience.
To learn how to leverage contact angle measurements in new product development or bonding, coating, and cleaning operations, download the eBook - The Advanced Guide to Transforming Product Development Through Surface Intelligence Data & Technology.