Our relationship with our vehicles may have changed in the past few months, with the idea of commuting to work looking more like a shuffle to the desk across the room rather than a drive to the office across town. However, cars have not dropped in prominence in our society.
With health risks now inherent to ride-sharing and mass transit, people who hadn’t really considered a personal vehicle are rethinking their position. When buying a car, it's a good time to consider safety, so it’s a good time to look at some of the mechanisms that are at the heart of the most recent advancements in vehicular safety systems: sensors.
Sensors are increasingly found all over car bodies. From backup cameras to LIDAR (a light-based radar system and an abbreviation of light detection and ranging) mounted on windshields, cars are decked out from bumper to bumper with technologies that need to “see” what is happening around the vehicle.
Vehicles equipped with adaptive cruise control systems and other driver-assist or safety features are like self-driving lites. All of these mechanisms have been designed to create a true AUTOmobile.
Rethink your adhesion manufacturing processes with Surface Intelligence.
One of the big reasons we only have these partially autonomous vehicles is because of the reliability factor. For cars to be able to drive themselves, these sensors would have to be perfect. They need to generate a continuous and accurate data stream regarding the constantly changing conditions around the vehicle. The sensors must maintain the integrity of the AI data by operating consistently, every day, without fail or deterioration. The ability of the car to self-drive is completely compromised if any of the sensors is diminished in its data collection capabilities.
Right now, drivers can still respond appropriately to alerts regardless of how accurate they are because they can apply their own senses to react to obstructions in the road or adapt their driving to weather conditions. It’s a collaborative effort between the driver and the sensors to create a safe experience. We simply do not trust the integrity of the sensors' information enough to remove human intuition from the equation.
Think how protective we need to be to ensure the longevity of our phones. We can’t leave them outside and expect the lens on the camera to work as well as the previous day. Car sensors are very similar but massively more important and vulnerable.
Car sensors are close to the ground, have grime and mud slung on them, get rained on, iced over, and put through extreme heat and hours of direct sunlight, yet they need to operate flawlessly.
Much research is being conducted to determine the best ways to preserve these sensors and make cars as safe as possible. For the types of sensors already in wide use, a good place to begin understanding the complexity of the problem of protecting these systems is to look at the coatings applied to the sensors' lenses.
How to Keep Sensors Clean: Let Them Clean Themselves
If a sensor is going to stay clean, it either needs to repel dirt or self-clean. The vehicle operator is not expected to do anything other than turn a key or push a button and go. There is no expectation that a driver will be cleaning off sensor lenses, especially not if sensors are numerous and in difficult-to-reach places (i.e., under or behind the grille).
Sensors commonly have small plastic housings mounted to the vehicle, with the camera or radar component protected by a transparent lens. This lens is the sensor’s first line of defense against the elements. One of the best ways to ensure these lenses properly guard the sensitive equipment behind them is to apply a coating designed to remove disruptive particles that will inevitably land on the lens. These “self-cleaning” coatings are crucial to the life and performance of these sensors.
Self-cleaning coatings come in two varieties and serve distinct yet equally important functions. There are hydrophobic coatings and hydrophilic coatings, and which one you choose depends on how you want the water and moisture to interact with the surface of the lens and remove dirt and dust.
Hydrophobicity and hydrophilicity refer to how liquids behave when they come in contact with a surface. Water will spread out and “wet” a hydrophilic surface. If the glass isn't perfectly clean, water “beads up” on the surface as it dries, and dirt and minerals that were dissolved in the water appear as water spots.
However, the water runs off in sheets if the glass is clean. As the water dries on clean glass, it remains spread out, and any dirt or minerals are left as a thin, uniform (and invisible) film that doesn't interfere with the ability to see through the glass. Hydrophilic sensor coatings function similarly: water tends to run off in sheets, taking most of the dirt and dust with it. The thin, uniform film of water that remains and evaporates is spread out and doesn't leave behind water spots to obstruct the sensor’s ability to image its surroundings.
Hydrophobic Coatings on Lenses to Repel Water and Clean Away Dirt
A hydrophobic coating does the exact opposite of a hydrophilic coating. These coatings effectively repel water, causing it to bead up and roll off the surface. These balls of water pick up dirt and dust particles as they roll along, carrying them right off the lens surface. Because of this, hydrophobic coatings are self-cleaning and can be very effective at maintaining a pristine lens. They are much more commonly used on the exterior of lenses than hydrophilic coatings.
When these coatings are applied during the manufacturing process, tests need to be conducted to ensure that they are properly water-resistant and evenly coated. A simple water contact angle measurement is the perfect metric for manufacturers to understand these important characteristics of their coatings. Contact angle measurement devices, like the Surface Analyst, deposit a drop of water on a surface and measure the extent to which that droplet wets out (indicating hydrophilicity) or beads up (indicating hydrophobicity).
A high contact angle correlates to a surface that repels water and has a low amount of what is called surface energy. Contact angles are highly sensitive to minute changes in surface energy, so it’s easy to know if a coating is actually sufficiently hydrophobic. This process control method is also useful for measuring the lens surface is cleanliness before applying the coating to ensure it will create a firm, reliable bond with the lens material. When a coating cannot bond properly or uniformly, it can delaminate, which makes it very hard to protect the lens from dirt.
Seal Sensors
To keep sensors out of reach of anything that might be able to weaken their ability to sense what’s going on around them, the housings they live in need to be hermetically sealed. This means no vapor of any kind can get in. Clean, dry air must be captured behind the lens when applied to the housing, and the seal must prevent any gas exchange with the outside environment.
If these seals are created through adhesive bonding, the materials to be bonded will go through a treatment process, frequently with plasma, to create a high-energy surface. When a surface has high energy, it will have a low contact angle measurement, and the surface will be very reactive and eager to bond. When the adhesive is applied to the lens and housing, it will form strong bonds with the chemically reactive surfaces to ensure the sensor is completely enclosed.
One of the reasons a reliable seal is so important is that these sensors are essentially in the splash zone. If mud gets splashed onto your sensor, it can render it completely useless. Many car manufacturers are creating creative ways to rinse off sensors using cleaning fluid jets focused on the lenses that work similarly to windshield wiper fluid. But if the sensors are bombarded with grime, water, and cleaning solution all day, the seal must hold strong through it all.
But what happens if something creeps through?
Keeping the Interior of Lenses Clean with Hydrophilic Anti-Fogging Coatings
Anti-glare and anti-fog coatings on the interior of lenses protect the sensor’s ability to see clearly, even if the housing seal allows moisture inside.
When moisture condenses on the inside of a hydrophobic lens, it beads up into tiny droplets that scatter light: we call this "fogging up.” Anti-fog coatings create a high-energy (hydrophilic) surface on the inside of the lens, which allows water to spread out and not bead up; the lens may have a thin film of condensed water on it, but it remains clear. However, the high surface energy of anti-fog coatings presents its own problem.
High-energy surfaces are extremely reactive and tightly adsorb all sorts of contaminants and soils. This surface (like dirty glass) will no longer sheet off the water the way it needs to, so typical hydrophilic coatings used for anti-fogging can have a relatively short lifespan.
To overcome this conundrum, coating manufacturers include a tiny bit of surfactant in the coating. When moisture condenses on the lens, it dissolves some of the surfactant, lowering the surface tension of the water and allowing it to spread. So, this approach focuses on lowering the surface tension of the liquid. When the water that absorbed the surfactant evaporates, it leaves the surfactant behind to fight another day.
So, these lenses need to be anti-fogging and long-lasting. It's important to have quantitative tests to ensure the coatings are acting properly: that the surfactant built into the coating is, in fact, migrating out of the bulk of the coating in sufficient quantity to ensure that the surface tension of the liquid is reduced. The liquid spreads out, and the sensor chugs along undeterred. A great way to measure the effectiveness of these coatings is by using the “dynamic wetting,", which quantifies the presence and activity of surfactant on a surface.
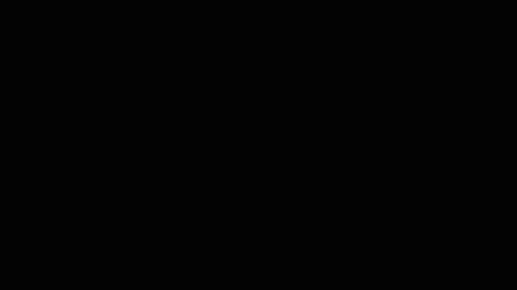
In the video above, you can see how the water continues to spread out on the surface that has a surfactant present. In some instances, manufacturers must be certain their surfaces are surfactant-free (such as a FIPG sealing application). In the case of sensor coatings, sometimes the presence of a surfactant is exactly what is called for.
Manufacturers equipped with technology that accurately measures the existence of all kinds of substances on their surfaces have a clearer view of each assembly's potential for failure or success.
Optimize the power of next-gen connectivity with data & surface intelligence.
Learn more about how your organization can leverage the power of water contact angle to drive innovation, optimize existing processes, and design with more freedom; download the eBook "The Future of Manufacturing: A Guide to Intelligent Adhesive Bonding Technologies & Methodologies."